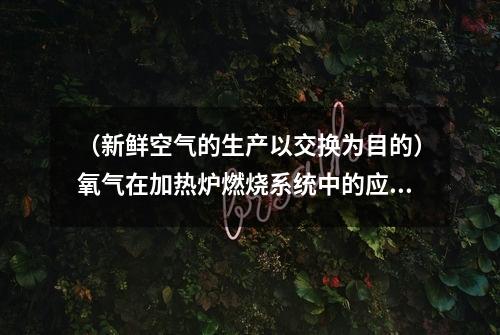
今天窝牛号就给我们广大朋友来聊聊新鲜空气,以下关于的观点希望能帮助到您找到想要的学习。
再热炉的主要功能是将半成品钢(钢坯、大方坯、板坯或圆钢)的温度通常提高到1000摄氏度至1250摄氏度之间,直到其塑性足以在热轧机中轧制出所需的截面、尺寸或形状。出于冶金学和生产力的原因,再热炉也必须在加热率方面满足具体要求和目标。在再热炉中,有一个连续的材料流,当它通过炉子时被加热到所需的温度。
热轧作业需要以最低的成本和轧机的最佳生产获得高质量的再加热半成品钢。热轧厂用于加热半成品钢的再加热炉消耗大量的能源,同时产生大量的污染物。正因为如此,有必要研究如何减少能源消耗和污染物,从而减少成本。这可以通过提高再加热炉的燃料效率来实现。
复热炉的燃烧系统对复热半成品钢的质量和复热所需的燃料量都有重大影响。今天,人们对再热炉的重要期望不仅是降低污染物的排放和能源消耗,而且还希望提高被加热钢铁产品的质量、可靠性、均匀的温度、热流以及设备和人员的安全。所有这些都是对再热炉的燃烧系统有相当大影响的关键因素。
启动和维持燃烧所需的三个基本要素是:(i)燃料,(ii)氧气和(iii)用于点火的足够能量。如果燃料和氧气能够不受任何限制地相遇并发生反应,燃烧过程是最有效的。然而,在实际的加热应用中,仅仅考虑有效的燃烧是不够的,还要考虑到传热方面。以下是重新加热炉中燃烧系统的重要参数。
需要传给炉料的热量。
炉内产生的热量不仅需要加热炉料,而且还需要克服所有的热量损失。
将部分可用的热量从炉内气体转移到加热炉料的表面。
炉料内部温度的平衡。
炉子里的热量通过门和墙等损失。
由废气携带的热量。
由废气引起的污染物(如氮氧化物等)的排放。
由78%的氮气和1%的氩气稀释的氧气组成的空气并不能为燃烧和传热提供最佳条件。空气中的氮气在燃烧过程中被加热,为了避免转移到氮气中的能量损失,有必要回收这些能量,以节省燃料。
热量通过对流、传导和辐射转移到固体产品表面。产品内部的热量传递只通过传导。这意味着产品表面(加热时随时间变化)、半成品钢的尺寸和材料以及炉子的内部尺寸都很重要。
为了实现高效和均匀的加热,炉内的气体成分和流动模式也很重要。传统的、非优化的加热策略在稳定状态下可能是足够的,但在生产中断、产品等级或尺寸变化、或目标下降温度变化的情况下,不能提供最佳的质量和成本性能。在今天的情况下,需要一个解决方案,在所有条件下提供最高质量和最低成本的加热,对环境的影响最小。
如今,由于全球变暖,严格的环境法规要求尽量减少具体的燃料消耗,同时减少包括氮氧化物(NOx)在内的污染物。在满足生产要求的同时,最低能源消耗和污染物排放的目标相互冲突,这给操作人员和设备供应商带来了挑战,他们需要利用一切可用的技术来设计高效节能、符合环保要求的再热炉燃烧系统。
在传统的燃烧器设计中,这两个目标往往是相互冲突的。然而,使用最新的技术和带有扩散火焰燃烧技术的燃烧器设计,现在可以通过预热燃烧空气实现高水平的效率,并相应地减少氮氧化物的排放。
在钢铁厂中,有很多类型的再热炉正在运行。再生炉的结构由几个区域组成。再生炉通常设计有多个加热区,即(i)预热区,(ii)加热区,以及(iii)浸泡区。半成品钢片被送入预热区,并依次缓慢地移动到加热区和浸泡区。钢件在预热区和加热区大致被加热到目标温度,并在浸泡区浸泡,以保持整个钢件的均匀温度,钢件主要通过周围气体的辐射传热进行加热。每个区都有不同的目的,而且各区通常都有独立的燃烧器控制,即使燃烧的产物通过前面的区来排出烟道。空气与燃料的比例的设定通常是为了在烟气中产生一个理想的过量氧气水平。其目的是确保所有的燃料都在再热炉内燃烧,但同时也要避免燃烧空气过多而降低炉子的加热效率。
再热炉的多区结构使得燃烧优化非常困难,因为区间的相互作用、不断变化的产品要求、不断变化的提取以及提取棒材的行为本身。 有很多问题会导致最终结果的漂移。其中一些问题如下:
气体或空气的计量不准确
空气湿度的变化
大量的燃料或氧气从炉子的另一个区域迁移过来
在通过换热器预热空气的情况下,可能存在(i)管道或换热器的泄漏,(ii)温度校正系数失准,以及(iii)季节性变化
阀门和执行器的磨损或损坏
炉子的泄漏
此外,根据燃烧器的能力和所需的过量氧气水平,每个区都需要固定的化学计量比率。由于以下两个原因,各区的比例可能不同。
由于氧气水平、温度和水垢形成之间的关系,每个区所需的过量氧气可能是不同的。
由于燃烧器的混合能力不同,可能需要对不同的燃烧器转差率进行调整。
通常情况下,由于没有实时的过程反馈,再热炉的操作者不知道氧气是否达到或接近所需的设定点。在这种不确定性水平下操作炉子的后果可能是很严重的。考虑到燃烧器的反应和理论上的燃烧产物,可能会出现化学计量偏离设定点的情况。如果烟气中的实际氧含量超过了设定值,效率就会降低,增加不必要的燃料成本。如果实际氧含量低于设定值,那么一氧化碳含量就会增加,这就会造成不安全的操作条件,并由于未燃烧的燃料从炉子中流出而降低效率。此外,为了满足不断变化的炉子需求,再热炉中的空气-燃料比率控制器不断调整其设定点,因此氧化状态也一直在变化。在实践中,再热炉经历了某种程度的不完全燃烧。有几个问题会导致混合不良。这些问题在下面给出。
燃烧器效率
转速
空气和燃料的无可比拟
比率控制失调
炉子漏气
由于混合不良而造成的不完全燃烧也会导致一氧化碳和氧气的共存。在实践中,一氧化碳和氧气同时存在是很常见的。因此,再热炉的最佳操作需要通过合适的传感器获得实时的燃烧产物数据。
换热器通常用在再热炉中作为废热回收装置,以实现高热效率和节能。回收的余热用于预热燃烧空气,然后将其送入燃烧器。预热的空气导致了能源节约和良好的燃烧性能。然而,其缺点包括加入大规模的余热回收系统。此外,预热空气的温度通常最多只有600摄氏度到700摄氏度左右。
最近,在半成品钢的再加热领域有两个主要发展。这些发展是:(1)高温空气燃烧,和(2)氧气燃料燃烧。
高温空气燃烧
高温空气燃烧(HiTAC)技术利用超过1000摄氏度的预热空气。在再热炉中采用这种燃烧技术,可以使钢铁厂对同时减少能源消耗以及减少二氧化碳和氮氧化物的排放做出巨大贡献。与传统类型的炉子相比,利用HiTAC技术还可以减少再热炉的物理尺寸。
HiTAC技术的基本概念是,通过高循环再生器最大限度地回收废热,并控制高度预热的燃烧空气与燃烧气体的混合,产生均匀和相对低温的火焰。
HiTAC技术中使用的再生式燃烧器具有独特的燃烧特性。这些特性导致了高效和清洁的火焰,具有均匀的温度和热通量曲线。这些特性导致了生产率的提高和产品质量的改善,并为炉子部件提供了更温和的环境。 HiTAC技术可以使运行成本降低。
HiTAC技术在所有的燃料-空气混合物(包括非常稀薄的燃料混合物)中提供了明显更高的火焰稳定性,更高的传热,以及从烟囱中的低热量损失(废热)。该方法提供了一种利用适当的热交换方法将热量从高温侧(燃烧的气体)再循环到未燃烧的混合物侧的方法。预热给未燃烧的混合物提供了额外的焓值,而不会被燃烧产物稀释。
采用HiTAC技术后,火焰特征明显不同,火焰稳定,排放减少,并能显著节省能源。发现火焰颜色与通常观察到的蓝色或黄色有很大不同。在某些条件下,使用典型的碳氢化合物燃料已经观察到蓝绿色和绿色的火焰。相反,还观察到燃料的无焰(或无色)氧化。
以下是HiTAC技术的主要特点。
使用燃烧器中的再生器,以非常高的空气预热温度燃烧碳氢化合物。
废气产品的显热被用来加热燃烧空气(温度大于1000摄氏度)。该技术试图使空气预热接近目标炉温。
废气温度约为150摄氏度至200摄氏度。
提取燃料中的大部分能量用于加热过程。
有50%(替换冷空气)和30%(替换来自换热器的空气)的燃料节省。
炉内有非常均匀的热量分布。
氮氧化物的产生非常少。
在蓄热式燃烧器中,有一对配置,每个燃烧器在燃烧和排烟之间循环。助燃空气在燃烧器的两组通道之间循环。它通过一组进入,从燃烧器中的再生材料中获取热量。燃烧产物的气体通过另一组出口,将再生器材料加热到高温。在下一个循环中,燃烧空气和燃烧产物交换路径。
图1说明了HiTAC的概念,并与传统的再热炉燃烧作了比较。如果燃料和高温新鲜空气之间发生直接燃烧,通常会在炉子里产生极高的温度火焰。由于修改了炉子的几何形状,不仅基础火焰的熄灭是通过高速入口空气的剪切运动发生的,而且在燃烧前必须通过分离燃料和空气入口来稀释空气中的燃烧气体(BH)。需要注意的是,这些都是普通燃烧无法在环境温度的空气中持续的条件。此外,单独注入炉内的燃料也会在炉内夹带燃烧的气体,如果有的话,在这个准备阶段,燃料会发生一些变化,如热解、分解和液体燃料的汽化。燃料和夹带的产品(B*F)之间可能会发生弱的燃烧反应,而主要的燃烧则是在燃料和稀释空气的混合区发生的,其中有大量的燃烧气体(B*F*BH)。由于燃烧气体的高回收率导致氧气浓度低,火焰的变化可能会产生一个扩大的反应区,在那里可能会发生相对缓慢的反应。在没有预热空气的既定燃烧中,燃料和新鲜空气(F*A)之间的直接燃烧发生在燃烧器的近场。此后,在火焰的下游部分,由于再循环的燃烧气体被进入的燃烧空气夹带,可能会出现一些稀释状态下的燃烧。燃烧器附近的燃烧(F*A)显示出炉子里的最高温度,从炉子里排放出的大部分氮氧化物都是在这里形成的。然而,这个区域的燃烧对于维持炉内的燃烧至关重要,如果这部分发生熄灭,整个火焰就无法存在。
图1 采用HiTAC技术的混合和燃烧的概念
尽管使用了高度预热的空气,HiTAC的平均温度和瞬时峰值温度比普通燃烧要低得多。
全氧燃烧系统
全氧燃烧是指用氧气完全替换空气作为燃烧的氧化剂来源,而氧气可以通过低温技术或吸附技术产生。用氧气替换空气的一般优点是,几乎或完全消除了与空气一起带入燃烧过程的氮气量。减少燃烧中的氮气可以提高火焰温度和燃烧效率,因为较低的燃烧气体体积减少了从火焰中获取并流失到排气中的热量。因此,与空气燃料燃烧相比,使用全氧燃烧的优势如下:
减少能源消耗
提高加热率,从而提高产量(在不增加炉温设定点的情况下)。
减少炉子的排放
除上述优点外,与其他提高效率的方法(如换热器或排放控制设备)相比,使用全氧燃烧有时可以降低资本投资。由于更好的控制和更短的加热时间,全氧燃烧还可能导致更少的水垢损失。
与空气燃料相比,全氧燃烧的两种燃烧产物CO2和H2O的分压高得多。这提高了传热率。由于废气没有被氮气稀释,气相在传热过程中发挥了更积极的作用,这不仅是因为CO2和H2O的传热传导率和热容量更高,而且还因为它们都是高热辐射的三种原子气体。
与空气燃料相比,全氧燃烧炉的流动模式是有利的。由于没有氮气的存在,并由于节省了燃料,废气量减少了70%至80%。因此,气体的停留时间更长,有更多的时间将热量传递给产品。事实上,产品被浸泡在由二氧化碳和水组成的气态废气中,也就是说,湿润的环境具有更高的传热能力。
当比较纯氧炉和空气燃料炉时,两者都设置在相同的炉温下,材料在纯氧炉中更快达到设定值。这是因为气体的特性。
与空气燃料燃烧相比,全氧燃烧的可用热量大大增加。可用热量的增加与能源消耗的减少和炉子产量的增加直接相关。
可利用的燃烧热量的增加意味着更少的热量损失到废气中,总能量输入的更大比例被留在再加热炉中做功。因此,当可用热量增加时,做恒定数量的工作所需的总能量输入量就会减少。
节能效果因燃料类型、现有燃烧比和燃烧空气温度而异。其他因素,如烟道口尺寸的减少和辐射损失,会影响全氧燃烧的实际能量减少率。全氧燃烧提高燃烧效率的另一个影响是能够提高加热率,获得更多的炉子吞吐量。
产量增加的实际限制取决于半成品钢材料的吸热能力以及半成品钢材料受热的时间和温度。各种氧燃气装置的经验表明,在大多数操作中,材料吞吐量可以增加,而不需要增加炉子的温度设定点,但已经满足设定温度斜率限制的炉子除外。除了可用热量的增加,更高的全氧燃烧火焰温度和燃烧气体的辐射潜力对加热能力和生产率有积极影响。
氧燃料火焰温度一般比空气燃料火焰温度高500摄氏度至800摄氏度。由于辐射传热取决于从源头到接收器的温度差的四次方,全氧燃烧导致火焰对物质的辐射势大幅增加。全氧燃烧的燃烧产物也是更好的辐射传热来源。这是因为空气燃料的燃烧产物大部分是氮气,它不像二氧化碳和水蒸气那样是一种有效的辐射传热机制,而二氧化碳和水蒸气构成了全氧燃烧的大部分产物。
在某些情况下,炉子的生产受到允许出炉的气体排放量的限制。全氧燃烧也可以成为减少炉子排放的一种手段,并允许在允许的排放上限内提高生产能力。
全氧燃烧的废气量大大降低。全氧燃烧的总废气量一般比空气燃料的总废气量少70%至90%。在很多情况下,仅废气量的减少就能带来好处,特别是在现有污染控制设备有限和/或颗粒物排放令人担忧的情况下。全氧燃烧的一个更重要的结果是降低某些废气成分的排放。使用全氧燃烧最明显的结果是减少了燃料消耗。随着燃料消耗的减少,在一定时间内或每单位加热的半成品钢材料中,二氧化碳的排放也会降低。虽然二氧化碳的产生目前不是一个主要问题,但正在发生的全球变暖和气候变化表明,在即将到来的未来,更严格的二氧化碳排放条件可能是一个因素。很多炉子经营者更直接的关注是氮氧化物的排放。通过全氧燃烧,燃烧产物中的氮气分压大大降低,即使在火焰温度升高的情况下,也会降低形成氮氧化物的可能性。很多因素影响全氧燃烧炉的氮氧化物排放率。氧气产品的纯度就是这样一个因素。然而,最大限度地减少全氧燃烧氮氧化物排放的主要因素是炉压控制。二次空气泄漏与高氧燃烧火焰温度相结合,可以大大降低全氧燃烧作为氮氧化物控制技术的影响。
与空气燃料火焰相比,纯氧燃料火焰具有更高的温度,而体积和长度却更小。在设计应用于钢铁材料再加热的全氧燃烧器系统时,需要考虑全氧燃烧器的火焰特性。一般来说,钢铁的再加热需要均匀的温度分布,以避免在再加热的钢铁产品中出现局部过热或加热不足。全氧燃烧器的类型和位置取决于再加热炉的类型以及火焰与半成品钢材料的接近程度。
燃烧产物的再循环促进了气体在加热室中的运动,从而使温差最小化。另外,燃烧气体再循环进入氧燃气火焰,降低了火焰的峰值温度,促进火焰辐射曲线更加均匀,以保护最靠近燃烧器的产品不会被过度加热。有几种纯氧燃烧器的设计可以获得再循环的效果,包括获得专利的喷嘴以及其他利用纯氧火焰动力产生气体再循环的设计。
在为效率提供巨大好处的同时,全氧燃烧的低量燃烧产物在设计燃烧控制系统时需要一些特别的关注。燃烧比的适当控制对于再加热过程至关重要,因为燃烧的产物构成了加热气氛,并最终影响到水垢形成的和类型。在空气燃料燃烧系统中,与空气一起进入燃烧过程的大量氮气提供了一个阻尼器或安全因素,以防止空气与燃料比率的变化。在全氧燃烧中,这种阻尼器几乎完全被消除了。这意味着全氧燃烧中氧气与燃料比例的百分比变化对加热炉气氛的影响比空气燃料燃烧的相同变化要大。
与空气燃料燃烧相比,全氧燃烧对炉内气氛的良好控制需要控制系统有更高的精确度。通常需要进行质量流量补偿,以满足全氧燃烧保持良好炉内气氛的精度要求。全氧燃烧控制的另一个重要变量涉及炉子排气和压力控制系统。
全氧燃烧的废气量比空气燃料燃烧的废气量减少10%至30%,这取决于热效率的提高。这意味着现有的用于控制空气燃料燃烧的炉子压力的设计,在大多数情况下不足以在转换为全氧燃烧时保持良好的炉子压力控制。具体来说,在空气燃料燃烧中使用的较大的烟道口和风门尺寸的压力控制仪器的控制范围减少到对全氧燃烧的排气量无效的程度。因此,在转换为全氧燃烧时有必要减小烟道口尺寸,或者在设计新的再热炉装置时对较低的排气量进行补偿。缺乏良好的炉压控制会导致三级空气泄漏,这可以为额外的氮氧化物形成提供氮源,从而最大限度地减少或消除减少排放的可能性。进入再热炉的空气泄漏也会影响炉内气氛,给钢材表面质量控制带来麻烦。
不管是哪种类型的燃烧系统,水垢形成的和类型是钢铁再加热炉操作的一个重要考虑因素。除了钢的合金类型外,炉内气氛和加热是制约水垢形成的主要因素。为了保持对水垢形成和钢材表面质量的控制,需要对燃烧比和炉压进行良好的控制。然而,即使在理想条件下,全氧燃烧产生的气氛也与空气燃料燃烧的气氛不同。
今天的内容先分享到这里了,读完本文《(新鲜空气的生产以交换为目的)氧气在加热炉燃烧系统中的应用》之后,是否是您想找的答案呢?想要了解更多,敬请关注baike.ccv168.com,您的关注是给小编最大的鼓励。
本站所发布的文字与图片素材为非商业目的改编或整理,版权归原作者所有,如侵权或涉及违法,请联系我们删除
热门信息
阅读 ()
1 注册微信号怎么注册第二个阅读 ()
2 怎么把照片变成卡通头像阅读 ()
3 手机越充越少电怎么解决